Market Unit Composites
Composites is the competence center of RENOLIT for the production of thermoformable sheets and panels.
The Market Unit produces plastic composites in the form of rolls, sheets and honeycomb panels with divers polymeric, natural and mineral raw materials for the manufacture of, for example, automotive interior trim parts, building formworks and other customer-specific solutions where light weight, formability, mechanical performance and recyclability are key parameters.
Furthermore our products are used for applications in the construction industries as well as other industrial areas.
Recyclability
Our products are 100% recyclable.
We offer our customers the possibility of taking back discarded thermoformed
trim, which result from the processing of our products. This scrap material can
be granulated and re-introduced into the extrusion process.
Extrusion -> Thermoforming -> Recycling
The scrap milling can be implemented close to the thermoforming process line. We are available to cooperate to install a milling machine close to the line to make the regrind material to be collected in big bags and shipped to our company.
Process optimization
Thanks to our more than forty years experience, RENOLIT engineers define the right process parameters together with the customer minimizing scrap and increasing the efficiency of the production. Upon request, all the optimization actions can be performed at the customer manufacturing site.
Mold supplier support
Composites cooperates with the best mold suppliers to reach the right mold definition. For the tooling design and manufacturing for our classic WPC sheet RENOLIT WOOD-STOCK we worked with all the main mold suppliers in the sector.
Mold testing area
In our plant in Buriasco (Italy) we have the possibility to define the mold and/or test a prototype using a manual production line with an infrared oven and a press. By the use of a prototype tool made out of wood, we can offer a very fast and economical production of prototypes.
Further processing support
We work with other industry specialists to develop a total package for you.
Thermoforming Advantages
One-step process
High formability
Can join different covering materials
Glue free
Different type of cutting
Can obtain very deep drawn shapes
Dimensional stability of the finished part
Inserts made of various materials
Fast Cycle
Simple tooling
100% recyable
The Locations of Composites
Automotive
Lightness and recyclability combined with outstanding technical
characteristics make our Polypropylene composites the material of
choice in the automotive industry.
Applications
Building
Our sheets have been designed to obtain the best performance in the building industry.
We developed a special sheet for formworks applications. Even though we offer a
wide range of sheets for diverse building applications.
Applications
Panels
With its outstanding properties our versatile RENOLIT GORCELL panels impress in every area.
Applications
Our Contact Persons for you
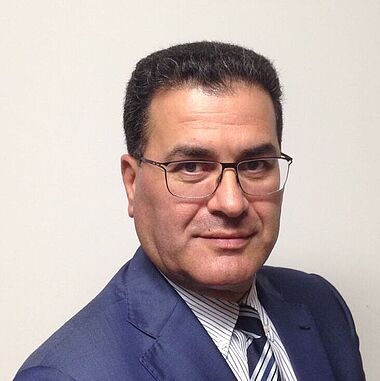
Ulisse D'Eramo
General Manager SMU Composites
Fax: | +39.0121.56323 |
Mobile: | +39.327.6318406 |
Email: | Ulisse.Deramo@renolit.com |
Address: |
Via Pinerolo 7, 10060 Buriasco (TO) Italy |

Rahul Chivate
(Managing Director APPL GOR India)
Email: | rahul.chivate@applgorindia.com |
Address: |
APPL GOR India 680/2 Pune-Nagar Road |

Regine Koudela
Head of Sales & Marketing Mobility
Fax: | +39.0121.56323 |
Mobile: | +39.345.5889578 |
Email: | regine.koudela@renolit.com |
Address: |
Via Pinerolo 7, 10060 Buriasco (TO) Italy |

Alfredo Sellitti
Head of Sales & Marketing Formwork
Phone: | +39.0121.569554 |
Fax: | +39.0121.56323 |
Mobile: | +39.345.0598339 |
Email: | alfredo.sellitti@renolit.com |
Address: |
Via Pinerolo 7, 10060 Buriasco (TO) Italy |

Raffaella Giovannini
Head of Sales & Marketing Non Automotive
Phone: | +39.0121.569529 |
Fax: | +39.0121.56323 |
Mobile: | +39.324.6624773 |
Email: | raffaella.giovannini@renolit.com |
Address: |
Via Pinerolo 7, 10060 Buriasco (TO) Italy |

Jim Lyon
Technical Sales Manager Composites NAFTA
Phone: | +001.563.580.4979 |
Email: | james.lyon@renolit.com |
Address: |
RENOLIT Gor S.p.A. 2935 S Fish Hatchey Road #355 Madison, WI 53711 |